What are Basic Configuations for ZZHZ Safety Monitoring System of Bridge Girde Launcher?
What are Basic Configuations for ZZHZ Safety Monitoring System of Bridge Girde Launcher?
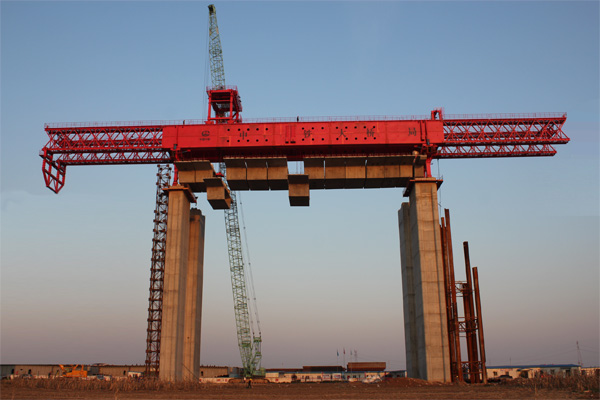
To meet customer's requirements, ZZHZ has developed a series of safety monitoring system for birdge girder launcher. Basic configuations are as following:
1. Signal Source:
Sensor for weight, height, stroke, wind-speed and etc.
2. Weight Sensor:
Pin roll will be used. By testing the load-carrying capacity of steel wire rope, signals will be transmit into PLC. After processing data will be displayed in the touch screen and storied.
3. Height Rotary Optical Encoder:
It will be installed on the output shaft for trolley moving system.The distance of trolley moving will be calculated by testing the rotary speed of trolley moving. Analog signal will be transmit into PLC over cable. After processing the data will be displayed in the touch screen and storied.
4. Traveling Distance of Trolley Moving System:
It is installed horizontally on output shaft. The distance of trolley moving will be calculated by testing the rotary speed. Analog signal will be transmit into PLC over cable. After processing, the data will be displayed in the touch screen and storied.
5. Air Velocity Transducer:
Applied to test the wind speed of bridge construction site, air velocity transducer is installed vertically on the main beam of trolley. Analog signal will be transmit into PLC over cable. After processing, the data will be displayed in the touch screen. If wind speed is over the limit 5 seconds later, the wind alarm will cut down the main power automatically and the final data will be storied by the supervision system.
6. Levelness Tilt Angle Sensor:
It is installed horizontal on the main girder of the launching gantry, which is used to test the stress status of main girder during construction. Analog signal will be transmit into PLC over cable. After processing the data will be showed on the touch screen. If it exceeds the limit level, there will be alarm arising to alert load shedding. The data will be memorized.
7. Perpendicularity Tilt Angle Sensor:
Applied to test the stress status during construction, perpendicularity tilt angle sensor is installed on the outriggers of launching gantry. Analog signal will be transmit into PLC over cable. After processing the data will be displayed in the touch screen. Should the data exceeds limit, alarm will inform workers in site to decrease carrying load. The data will be storied.
8. Operation Command Signal:
The supervisor system will connect the operation signal of electric control panel with PLC. After data processing operation location will be displayed on touch screen. The information can be storied.
9. Touch Screen:
Installed on the operation panel, touch screen can display status of different components of launching gantry. It can also find history statistic includes traveling, operated and alarm record.
ZZHZ Related Products:
Gantry Crane, Overhead Crane, Bridge Girder Launcher, Girder Transporter, Concrete Batching Plant, Concrete Mixer and etc.
See more, please visit our website: zzhz.com
Email: zzhz114@gmail.com Tel: 86-371-68000000