Maintain the Tired Gantry Crane
(1), The machinery parts:
The supporting motor, reducer, electrical hoist and the other parts must be maintained as the instructions leaflet provided by the manufacturers. The bearings installed on the traveling mechanism and the moving and fixed pulleys should be filled with the Calcium-based grease monthly. The lubrication oil for the reducer needs to be replaced every three years. And the brake system of the electrical hoist must be checked every week. Test the brake function when we operate the machine every time in order that we can guarantee its reliability. To prevent the dust, sand and other dirty objects hinder the performances of the sprocket wheel and chains installed on the traveling mechanism, it’s essential to clean them frequently to avoid damaging the sprocket wheel and other parts.
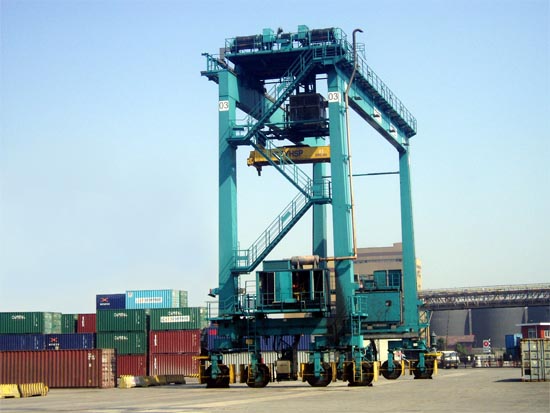
(2), The maintenances of the steel rope and pulleys
Inspect the steel rope to find if there are phenomena of the broken wires and loosed strands, replace them once the similar conditions exist. The maintenance of the steel rope must be strictly carried out in terms of GB/T14406—93<< The general purposed gantry crane>>. Frequently check the pulleys to ensure that they run normally, no abnormal noise, and deal with it immediately when any extraordinary phenomenon occurs. Check the connection condition between components, tighten the loosed parts. Besides deal with the loosed bearing pins and cotter pins as soon as possible.
(3), How to maintain the steel structure?
Strict inspection before the gantry steel structure begins to put into use. If the welding seam has been found the break, out of shape, look for the reasons and contact the manufacturers timely. Then deal with them as per the producers’ repaired program. Repair the seriously deformed members before using them again. Paint the steel mechanism every year, remove the greasy dirt, moisture content and other additives that will affect the paint on the steel surface before painting.
(4), How to maintain the electrical control system?
The operators must inspect the electrical components regularly carefully and seriously. For example: if the test button on the air switch can tripping operation normally; if the contactor can contact well and no abrasion; if the over-current relay, intermediate relay and limit switch connect well. Don’t put them into use before eliminating all the hidden dangers and problems. Every time when we finish the work, the operators must shut off the main switch, close the electrical appliance box to prevent the rainwater intrusion which may cause the electric shocks or damage the electrical components.
(5), The transportation and safekeeping of the machine
Regarding the transportation and safekeeping of the electrical components, it had better be in the ambient temperature (-25~+55℃). To prevent any damage, the measures for moisture-proof, anti-vibration, shock protection need to be prepared ahead of time.
(6), Regular inspection
1, The daily inspection before we start every time
Check the connection bolts on the steel structure (main girder, supporting legs). Check the electrical hoist, appliance, steel rope and so on. Check the sprocket wheel and chains of the traveling mechanism to ensure its moving safely. Check the electrical appliance control box, cables, limit switch, alarm system and brake system etc.
2, The routine inspection and maintenance every week
Ensure the clean of every lubrication part and refill it timely. Do a completely inspection on all these parts, avoid the break on the welding seam. No abnormal noisy and phenomenon occur when the motor, electrical hoist and generator is operating.