How to Use and Maintain in Run-in Period
Hoisting Machinery: How to Use and Maintain in Run-in Period
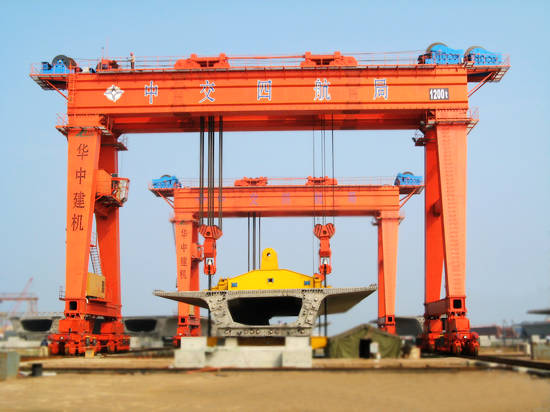
What is a run-in period?
Run-in period, also called first-used period after leaving factory, which is stated according to the initial technical features of mechanical equipments. As to hoist machinery, there is always 60 hours run-in testing time to keep it in good condition, decrease failure rate and enlarge working life. However, due to time limit for the construction project or in order to gain revenue as soon as possible, some people may ignore the special technical standard and adopt overload use during the 60 hours run-in period, which will give rise to frequent infancy failure for hoisting machinery. Even more, it will influence the engineering process. Therefore, we should pay more attention to the method of use and maintain during run-in period.
What are the Features of Run-in Period?
1. Fast Wear Rate
Influenced by components factors including processing, assembling and adjusting, the fabrication surface of new hoisting machine will be rough, the connection area of the fitting surface limited and the pressure-bearing condition uneven. Especially during operation, concave-convex parts of components’ surface will rub with each other and fallen metal scraps regarded as abrasive materials and go on the rubbing. Therefore, the rub speed will be faster if it is in the period of running-in time. Under such a condition, if the hoisting machine is working under over-load, it may cause broken components and early failure.
2. Poor Lubrication
Due to small fit clearance for the new components, it is hard to promise its homogeneity. Lubrication oil is hard to come into being even oil slick to prevent frication, so that it will reduce the oiling efficiency. Seriously, it may scratch the surface or cause occlusions with each other.
3. Looseness
The newly shaped and installed components have deviations on geometry and dimension, there may looseness happens sometimes. In the first-used period, impact, vibration, temperature deformation are the most important reasons to give rise to looseness.
4. Broken-down in Operation
If you don’t have enough professional knowledge or understanding, especially for green hands, mechanical accidents may happen.